Back to all posts
The request from the client
In March 2022, the first month after the Russian attack on Ukraine began, one of our clients called us, asking for help. "We have founded a charity fund. With our European friends, we now deliver hundreds of tons of humanitarian aid to Ukraine. But to keep it manageable, we need to add some automation."
At first glance, that was a trivial request. Our team had much experience in operational management and logistics automation. Of course, we were happy to use this experience to help the Fund in this mission.
But very soon, we understood that it was not trivial at all. All the experience from a peaceful life became irrelevant, and no standard business applications or Warehouse Management System could solve the problem.
So we had to reinvent it from zero.
BGV Charity Fund
The BGV Charity Fund was established as an urgent response to the humanitarian crisis created by the Russian invasion. Top executives of the Fund contacted their partners worldwide. And many companies, including Rossmann, Lidl, and Billa, responded by donating food, clothes, and medical supplies.
However, finding humanitarian aid was only the first problem. Another problem was delivering it to Ukraine and making this process manageable.
Overnight finance managers, lawyers, and investment analysts had to become logistics and warehouse specialists capable of building the supply chain from the ground in the new severe reality.
Challenges
In the war's first months, it was almost impossible to find proper warehouses. Even in the regions away from the battlefield, the available buildings were far from what is considered an industry-standard warehouse. Therefore, it was a significant success when they could find some space accessible by the trucks, with restricted access and the roof. However, usually, there was no proper equipment inside. Even electricity was not always available.
The lack of skilled warehouse personnel was another challenge. And the problem was on all levels, from people who physically moved the cargo to people who had to set up processes and manage them.
Finally, the incoming cargo was very diverse. Often, boxes were not marked with barcodes. And there were many mixed palettes with different goods and even categories inside.
At the same time, establishing proper inventory control was a crucial task. All necessary documents had to be in place, and the Fund had to be able to track each piece of cargo. First, donors expected transparency regarding the usage of their donations. Second, the Ukrainian government adopted special legal requirements to prevent the misuse of humanitarian aid, and the Fund had to comply.
In the beginning, Excel spreadsheets worked. However, that solution could not last long. On the other hand, the Fund did not have the time and budget to implement any industry-standard supply chain solutions.
Moreover, even if they would, all the standard applications require goods labeling, equipment, skilled personnel, and other absent things.
Solution
We started looking for a solution with the Fund team. After several attempts and failures, we eventually found the right approach that helped to overcome most challenges.
The process starts with people in the warehouse who print (on a consumer printer) individual labels and attach them with sticky tape to each pallet that arrives.
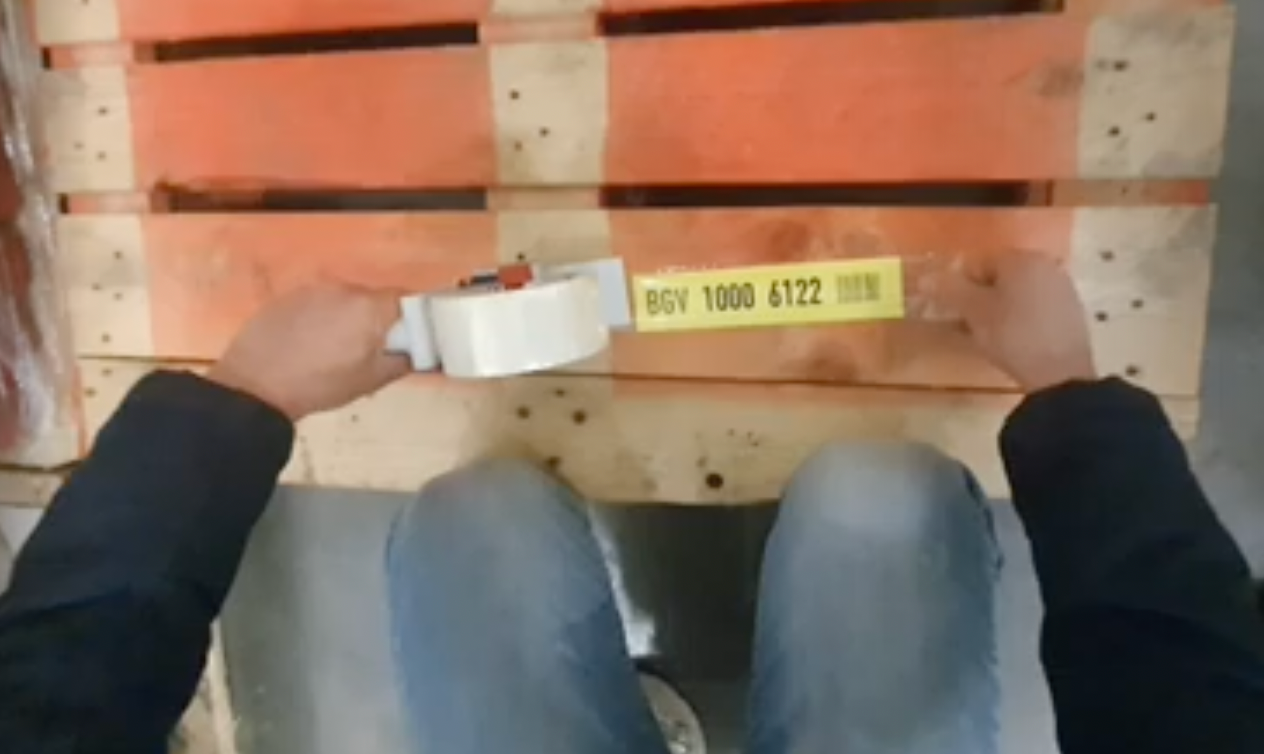
Then they take a picture using their smartphone. Finally, they upload the pictures to Google Drive. It is elementary, and people do not need any training.
And then the digital magic begins.
Our custom application checks the uploaded files, sends them to Google Vision, and does some sophisticated post-processing of the images. Then the application imports the images and creates all the lines with all the needed metadata. A manager in the office needs to review the data, correct it when necessary, and confirm the delivery.
When the cargo is sent to another warehouse or the aid recipient, it takes just a few clicks to record the transactions.
The process takes 10 minutes to complete, with manual work minimized and replaced by automation.
Sounds like an easy task? Indeed, the use of technology made it easy.
Labels and computer vision
The first element of the system is working with images. We designed a label that uniquely identifies each pallet.
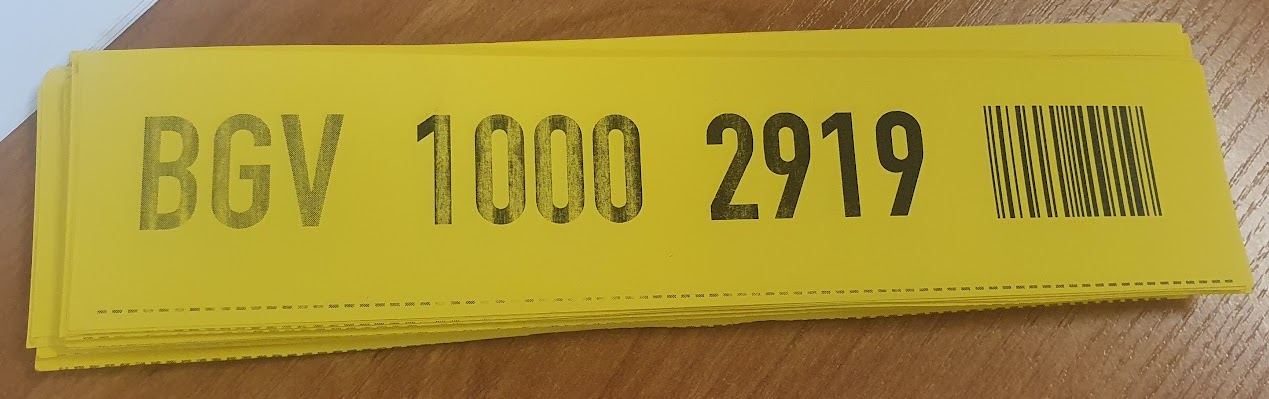
(In the picture, you see the label created on a printer with low toner. Still, it is suitable for computer vision)
It was optimized for three purposes at once:
1) People in the warehouse should easily read it from a distance without any equipment;
2) People with a barcode scanner should be able to use it to record the identifier quickly;
3) Computers should also read it easily.
The last requirement proved to become the game changer. No warehouses were equipped with simple barcode scanners. However, all the managers had smartphones with good cameras. So, it was not difficult for them to make pictures and upload them to the cloud.
We used Google Vision, a tool powered by Artificial Intelligence. It did a reasonably good job of recognizing the labels. However, it was not perfect. The actual recognition accuracy was about 70-80% which required more work from office workers. Also, the relatively high level of manual data entry created a risk of errors which we tried to avoid.
Nevertheless, with the help of custom programming, we achieved impressive 98-99% recognition accuracy, even in very unfavorable conditions. For example, the pallet in the picture below has eight valid bar codes and the folded label on its critical element, prefix. But it did not prevent the app from adequately identifying and recognizing the needed code.
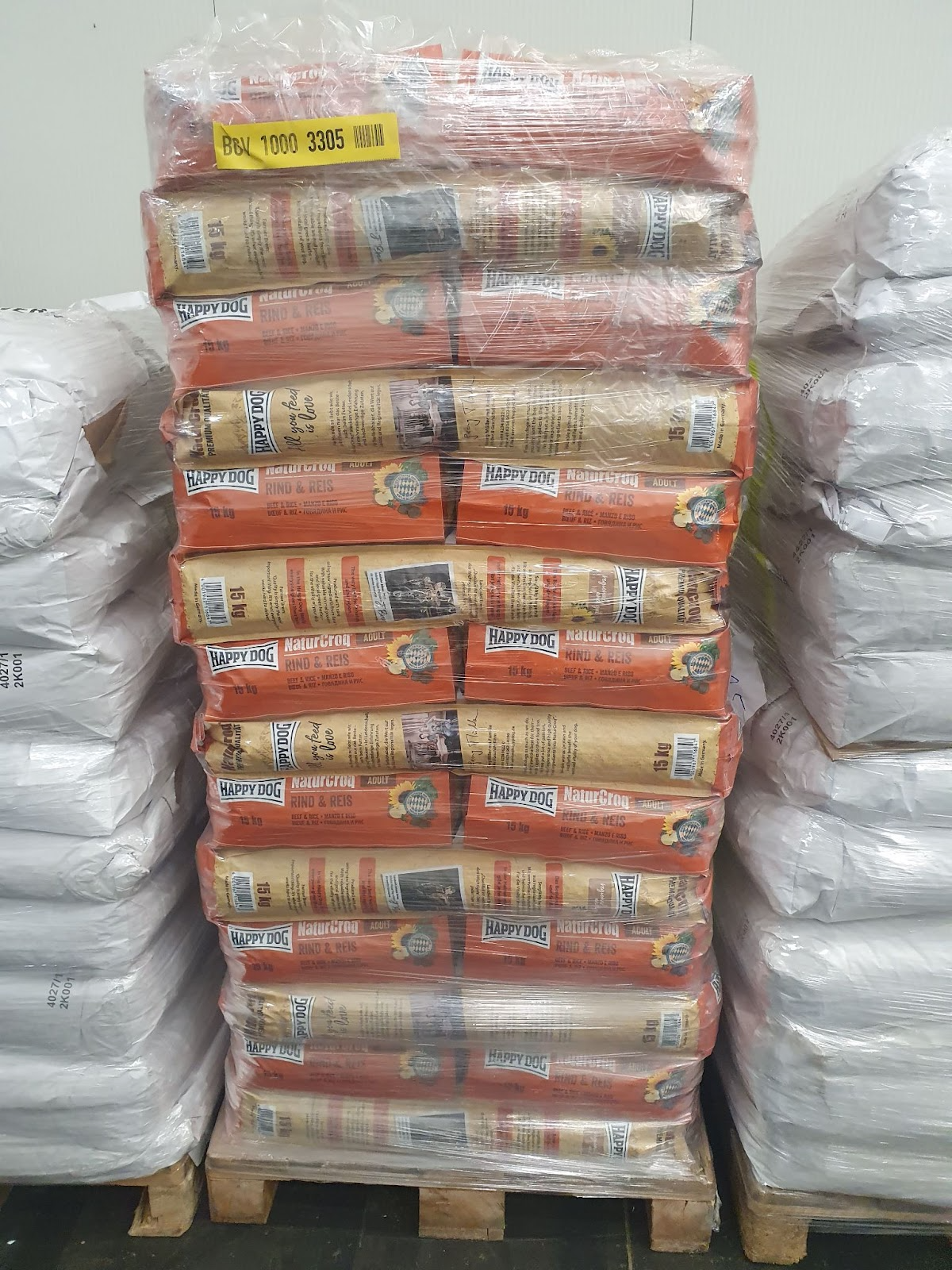
Logistics Application
The logistics application is a core element of the solution that allows tracking pallets from when they are received to when they are delivered. We implemented several delivery types, including the following
1. Incoming Delivery:
2. Transfers between Warehouses:
3. Outgoing Deliveries:
4. Inventory Count:
5. Repackaging:
In most cases, users only need to create a document and click a button to download images from Google Drive that automatically become records in the system. Today all the inventory control is executed by one manager doing it part-time.
And the application provides control over the inventory, not worse than sophisticated software packages developed by tech giants.
Low-code platforms
Caspio
We used Caspio to build the logistics application, as this no-code platform allows for building custom applications with incredible speed. It took us only two weeks to make the app, which is a great result considering the complexity of the task.
We selected Caspio for two reasons. First, Caspio actively supports Ukraine and kindly offered to use the application for free. Second and most important, Caspio is particularly good for this type of custom application.
First, it allows the development of interfaces that users find convenient and intuitive like in many standard business applications they work with.
Second, it is very suitable for reporting. Initially, we thought we would need to connect the application to PowerBI or Tableau. However, it proved unnecessary, as Caspio standard reports and pivots provide good data transparency.
Third, we connected this application with external systems (Google Drive and others) via Caspio API, and these applications started working as one product.
Finally, it works well under the load. For example, pictures of cargo for only one delivery can easily take 600 MB of space and even more. And all these files quickly and safely come from Google Drive to Caspio storage within a few minutes, creating zero problems for anyone.
Microsoft Power Automate + API
For the API integration, we chose Microsoft Power Automate for a few key reasons. Our client was already using Microsoft 365, and Power Automate is part of that package, making it a natural fit. It offers a flat fee, which is great because costs stay the same, even when we do more transactions. Plus, Power Automate is really good at automating complex tasks.
We used Power Automate to connect our app with other systems like Google Drive. This way, everything works together smoothly, like one product.
Conclusion
In business automation, usually, there are no unsolvable problems. Most problems that may look impossible often may be solved in different ways. And such solutions may be done quickly and without big budgets.
Today, any business can achieve much using no-code platforms empowered with Artificial Intelligence, decreasing the load on its employees and delegating routine tasks to machines.
It is already a year after we did the project. Now the Fund is working as a well-lubricated machine. During this period, they established five warehouses in two countries, totaling 10,000 square meters. In addition, they delivered over 300 trucks and 6,000 tons of goods. Also, they launched several new programs.
However, unfortunately, the war is not over yet. Therefore, the history of the Fund is not finished as well.
You may read more about our project in the Caspio blog post.
You may find more details about the Fund on its website and in this article. And if you need assistance in business automation, please, send us a message below 👇